The common point of AC servo drive and inverter is that the basic concept of servo is precise, precise and fast positioning. Frequency conversion is an indispensable internal link of servo control, and frequency conversion also exists in servo drives (stepless speed regulation is required). But a servo controls a current loop, a velocity loop, or a position loop, which is very different. In addition, the structure of the servo motor is different from that of the ordinary motor, which should meet the requirements of fast response and precise positioning. At present, most of the AC servo motors in the market are permanent magnet synchronous AC servos. However, these motors are limited by the technology, and it is difficult to achieve high power.
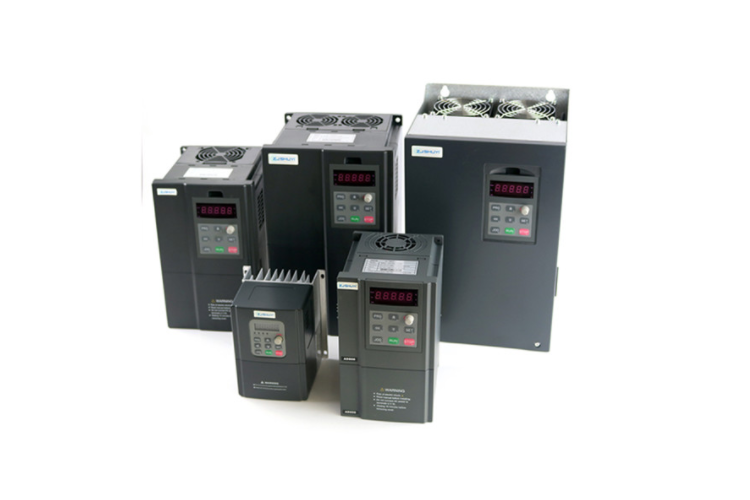
Synchronous servos of more than 10 KW are very expensive, so they are often used when field applications allow. AC asynchronous servo, many drives are high-end inverters with encoder feedback closed-loop control. The so-called servo is to meet the requirements of precise, precise and fast positioning. As long as it is satisfied, there is no dispute about servo frequency conversion. AC servo technology itself refers to and applies frequency conversion technology. It is based on the servo control of DC motor and is realized by imitating the control method of DC motor by means of frequency conversion PWM, that is to say, AC servo motor must have a frequency conversion link: frequency conversion is The AC power of 50 and 60 Hz is first rectified into DC power, and then passes through various transistors (IGBT, IGCT, etc.). ) is converted into a frequency-adjustable waveform through carrier frequency and PWM adjustment, similar to sine and cosine pulsating electricity. Because the frequency is adjustable, the speed of the AC motor can be adjusted (n=60f/p, n speed, f frequency, p pole pairs).
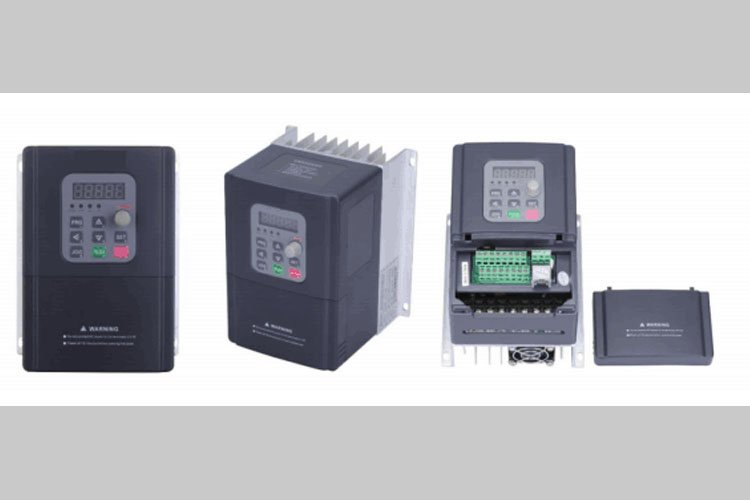
The specific difference between the drive and the frequency converter is:
1. Different definitions
The driver, also known as the servo controller and the servo amplifier, is a controller used to control the servo motor, and its function is similar to that of the inverter acting on the ordinary AC motor. It is part of the servo system and is mainly used in high-precision positioning systems.
A frequency converter is a power control device that uses the switching function of a power semiconductor device to convert a power frequency power supply into another frequency. It realizes the functions of soft start of AC asynchronous motor, frequency conversion speed regulation, improvement of running accuracy, and change of power factor.
2. Different overload capacity
In general, the drive has 3 times the overload capacity, which can be used to overcome the inertia moment of the inertial load when starting, while the frequency converter generally allows 1.5 times the overload.
3. Different control precision
The control precision of the drive is much higher than that of the frequency converter. Usually, the control accuracy of the drive motor is guaranteed by the rotary encoder at the rear end of the motor shaft, and some of the transmission systems have even control accuracy as high as 1:1000.
4. Different applications
Inverter and driver are two types of control, the former belongs to the field of transmission control, and the latter belongs to the field of motion control. One is to meet the requirements of general industrial applications, low performance requirements for applications, and the pursuit of low cost; the other is to pursue high precision, high performance, and high response.
Tel/Fax: 0086-577-62840011
WhatsApp: 008613355775769
#frequencyinverter #frequencyconverter #converter #inverters #vfds #vfdmarket
#ac-dc-acfrequencyinverter #solarinverter #3phasevfd, #acdrive,
#variablefrequencydrive #frequencyinverter #motorspeedcontroller
#goodqualityfrequencyinverter #variablefrequencydrive,