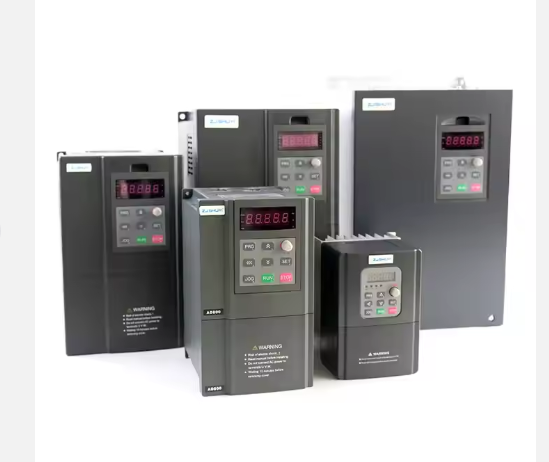
Introduction
In the realm of industrial automation, precise motor control is critical for optimizing productivity and reducing operational costs. Vector VFD (Vector Control Variable Frequency Drive) emerges as a groundbreaking solution, combining advanced vector control technology with variable frequency drive capabilities to deliver unparalleled performance. This article explores the core features, benefits, and applications of Vector VFD, highlighting why it has become the preferred choice for modern manufacturing, logistics, and process industries.
For more about our products, please click here.
Understanding Vector VFD Technology
Vector VFD represents a leap forward in motor control by integrating vector control (also known as field-oriented control, FOC), a technology that decouples torque and flux control for precise motor operation. Unlike traditional VFDs, which rely on voltage/frequency (V/f) control, Vector VFDs use complex algorithms to mimic the behavior of DC motors in AC motor systems. This allows for:
- Instant Torque Response: Immediate adjustment to load changes, critical for applications requiring rapid acceleration or deceleration.
- High-Precision Speed Regulation: Maintaining consistent speed even under varying loads, with speed accuracy often within 0.1% of the rated speed.
- Stable Operation at Low Speeds: Reliable performance even at frequencies as low as 0.1Hz, enabling smooth operation in demanding scenarios.
Key Advantages of Vector VFD in Industrial Settings

1. Superior Torque Control for Heavy-Duty Applications
Vector VFDs excel in high-torque environments, such as:
- Cranes and Hoists: Providing steady torque during load lifting to prevent sudden jerks or mechanical stress.
- Extruders and Conveyors: Maintaining consistent material flow by adjusting torque in real time as load resistance changes.This precision reduces equipment wear and tear, extending the lifespan of motors and connected machinery.
2. Energy Efficiency for Cost Savings
By optimizing motor speed and torque based on real-time load requirements, Vector VFDs can reduce energy consumption by 20–30% compared to fixed-speed systems. For example:
- In HVAC systems, they adjust fan speed according to air demand, eliminating wasted energy during low-load periods.
- In water treatment plants, they optimize pump speed to match water flow requirements, cutting electricity costs for 24/7 operations.
3. Reliability in Harsh Environments
Engineered for durability, Vector VFDs feature:
- Advanced Fault Protection: Monitoring for overvoltage, overcurrent, and overheating, with instant shutdowns to prevent damage.
- Wide Operating Range: Functioning reliably in temperatures from -10°C to +50°C and resisting dust/moisture (IP20 rating), ideal for outdoor or industrial floor installations.
4. Seamless Integration with Smart Factory Systems
Vector VFDs support multiple communication protocols (MODBUS, PROFIBUS, Ethernet), enabling:
- Remote Monitoring: Real-time data tracking of motor performance via SCADA or cloud platforms.
- Centralized Control: Integration with PLCs and HMIs for synchronized operation across complex production lines.This connectivity is essential for predictive maintenance and optimizing overall equipment effectiveness (OEE).
Applications Across Industries
Manufacturing
- Machine Tools: Ensuring precise spindle speed control for CNC machines, improving machining accuracy and surface finish.
- Assembly Lines: Stable conveyor belt operation with quick response to start/stop commands, minimizing material handling errors.
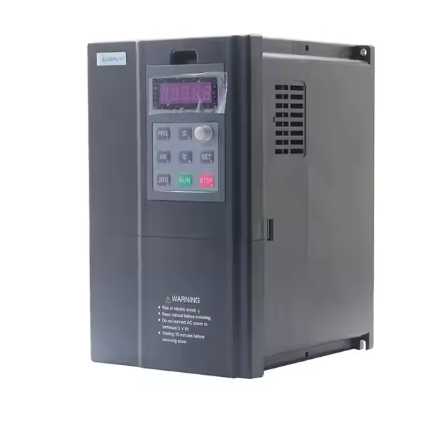
Energy & Utilities
- Wind Turbines: Converting variable wind speeds into consistent power output by adjusting generator speed.
- Compressor Systems: Maintaining optimal air pressure in industrial plants while reducing energy waste.
Logistics & Warehousing
- Automated Guided Vehicles (AGVs): Enabling smooth acceleration/deceleration for efficient material transport.
- Warehouse Cranes: Precise load positioning to enhance safety and productivity in high-throughput facilities.
Choosing the Right Vector VFD for Your Needs
When selecting a Vector VFD, consider:
- Motor Ratings: Ensure compatibility with your motor’s power (0.75kW–500kW) and voltage (200V–690V).
- Control Mode Flexibility: Some models offer both vector control (for high-torque) and V/f control (for basic speed regulation) for versatile applications.
- Environmental Requirements: Opt for models with higher IP ratings (e.g., IP54) if operating in extremely dusty or wet environments.
Conclusion
Vector VFD combines cutting-edge vector control technology with robust variable frequency drive functionality, setting a new standard for motor control in industrial automation. By delivering precision torque management, energy efficiency, and seamless integration, it empowers businesses to enhance productivity, reduce operational costs, and future-proof their infrastructure. Whether applied in manufacturing, energy, or logistics, Vector VFD solutions provide the reliability and performance needed to thrive in today’s competitive industrial landscape.
Web: www.shuyitop.com
Tel/Fax: 0086-577-62840011
Wechat/WhatsApp: 008613355775769
Zhejiang SHUYI Electric Co., LTD, Focus On Switches With 30 Years.