Inverter and frequency conversion principle of inverter
The process by which a frequency converter converts direct current to alternating current is called “inverting”.
Let’s talk about the inversion process first, which is divided into two steps.
Step 1: Convert DC to AC
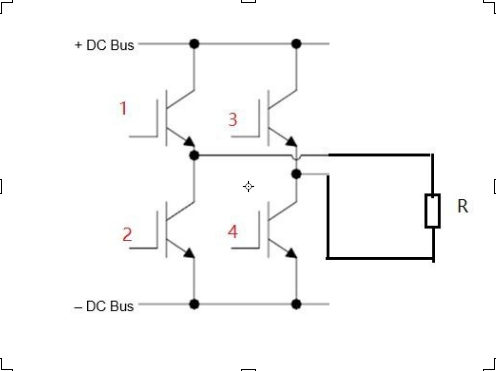
The above is a schematic diagram of a single-phase inverter.
1, 2, 3, and 4 in the figure are IGBTs. It has a feature that as long as we add a signal to its “gate G”, it can perform the “on” action, that is, conduction between CEs. If this signal is taken away, it can perform the “off” action, that is, the CE is turned off.
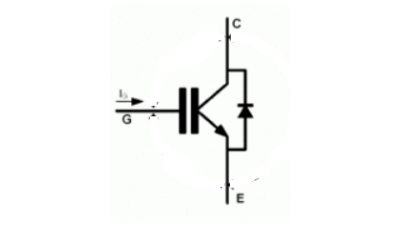
In the above schematic diagram, in the first half cycle, if we let the signal turn on the IGBTs of 1 and 4, but the IGBTs of 2 and 3 are turned off, then the voltage on the bus will pass through the load R, from the positive pole to the negative pole, to achieve R There is a downward current flowing through it.
In the second half of the next cycle, let the signal turn off the IGBTs of 1 and 4, and at the same time the signal will turn on the IGBTs of 2 and 3, then there will be an upward current on R.
In this way, the voltage on the load R is as shown in the figure below.

In this way, the “AC” transformation of the current is realized. As can be seen from the demo above, the voltage across R is a “square wave”. This voltage cannot drive our ordinary “induction” motor.
To drive the motor, you have to find a way to turn this “square wave” voltage into a “sinusoidal” voltage. How to change it?
Step 2: Turn the square wave into a “sine” wave.
If in a “half cycle”, we use technology to turn this “square wave” into a “sine” wave of half a cycle (0-π), then all the “inversion” work is completed.
This is achieved through a “PWM” (pulse width modulation) technique.
It is to use a triangular wave (carrier), and then modulate a sine wave (signal wave, modulation wave) onto this carrier. After such a modulation, a square wave signal with regular width and narrow width can be obtained. This process is called PWM.

The third step frequency conversion
With the previous inverter technology, let’s talk about frequency conversion.
Through this PWM technology, the frequency of the carrier wave does not change, and the frequency of the signal wave can be changed. Through the analysis of the second step above, the frequency of the output voltage is the same as the frequency of the signal wave. By adjusting the frequency of the signal wave, the frequency change of the output voltage is realized, that is, “frequency conversion”.
Careful friends will say: This actual waveform photo looks different from the one we simulated, and it is too different.
My answer is: the frequency of the fundamental wave used to simulate the waveform is too low. Count the peaks of the carrier wave in one signal wave cycle, 12, if the signal wave is 50Hz, the signal of this carrier is 600Hz. In order to get an approximately “equivalent” sine wave, the carrier frequency should be as high as possible. This is also easy to understand. But the frequency of this carrier can’t be too high, why can’t it be too high? I haven’t figured out the answer yet. When I think about it, I will write another article.
The switching frequency selection of the current IGBT is the result of a compromise under the premise of satisfying practicality. In the inverters I saw, the switching frequencies of IGBTs are 2kHz, 3kHz, and 5kHz.
Tel/Fax: 0086-577-62840011
WhatsApp: 008613355775769
#inverter #forfrequencydrive #ACvfd #frequencyinverter #ZJSHUYI #SHUYITOP
#variablefrequencydrive #threephaseacinverter #variablefrequencyinverter
#3phaseinverter#achotsalefrequencyinverter #highvoltageacinverter